If you’re currently using flexible intermediate bulk containers in a production facility, then you know it’s quite a monumental task moving bags throughout your facility. Moving empty bags, filling them up with product, moving them across your facility to ship and/or discharge; it can be quite the manual process involving a lot of labor. However, there are solutions that can significantly reduce the amount of manual labor required to do all these tasks while simultaneously improving the overall safety of your facility. We are talking about automated bagging systems.
It can be a bit confusing however, as ‘fully automated bagging systems’ often refer to a combination of different pieces of equipment working together to accomplish all of the tasks associated with using bulk bags. Because of this, we will examine some pieces of equipment we commonly see used in our customers’ facilities as well as the larger ‘fully automated’ systems these machines are a part of.
FIBC Filling Equipment
Filling equipment is a very common piece of automated bagging machinery. These machines are designed to efficiently and quickly load and fill a bag in a production line. Speeds can vary machine to machine based on type, brand, and/or fill specifications, however, generally speaking they can load anywhere from 30 to 40 bags per hour. For most facilities this is a massive speed upgrade versus manual filling and removes some of the dangers involved with handling bags and/or product more directly.
Fillers work by hanging the bag on a frame using the bags lift loops. The bag hangs below a fill hopper where the product is stored before entering the bag. A fill valve is then connected to the bags spout top (most fillers are designed to be used with spout top bags) and once secured, filling begins. When filling is complete the top of the bag is tied off and released onto a conveyor (if the production line includes a conveyor system) or removed by a forklift to be transported to a different part of the facility*.
*Note: Not all automated FIBC equipment is the same. The equipment described in this blog is commonly used equipment but does not represent all the various types of fillers, dischargers and other automated systems.
For more detailed information on the various types of filling equipment, check out this post.
Bulk Bag Unloaders (Discharge Equipment)
Unloaders or automated discharge equipment are another commonly used machine in facilities that utilize bulk bags. These machines are particularly useful in facilities that receive product already packed into FIBCs. They are designed to quickly and efficiently unload product stored in a bag either onto designated facility floor space, a production line, or another receptacle.
Shown on the right, an example of a Taylor brand unloader.
Unloaders work by using a forklift attachment and securing a filled bag to it. This attachment is then raised and secured to the discharge machine. The bottom spout of the bag (most unloaders are designed to be used with spout bottom bags) is then attached to the discharge valve on the machine and untied. At this point product should begin flowing into the discharge feeder. Another very useful and common feature of unloaders are massagers and/or bumpers to help the product keep flowing out of the bag. These work by slowly massaging the sides of the bag to keep product moving during discharge.
To see either FIBC fillers or unloaders in action, click here.
Fully Automated Systems
We now know what fillers and unloaders are but what are fully automated systems? Fully automated systems usually refer to the combination of multiple pieces of machinery that significantly reduce the amount of manual labor required to fill, discharge, and transport bags throughout a facility.
Common applications involve the use of an automated filler and/or unloader combined with a conveyor system to easily move bags during these processes. Combining these systems with forklifts significantly reduces manual labor requirements when using bulk bags. Less common but more advanced systems can include the use of pneumatic or flexible screw conveyor systems to transport product between each piece of machinery and/or throughout a facility.
Thanks for reading, check out our New Buyer's Guide!
It's our mission to make your bag buying experience easy, informative, and enjoyable. We also want to share our knowledge with you, so you can make the best purchasing decision for the company you represent. Our Buyer's Guide to Purchasing Bulk Bags is a great starting point for any decision. It contains critical information ranging from types of bags to important safety information about handling and transportation.
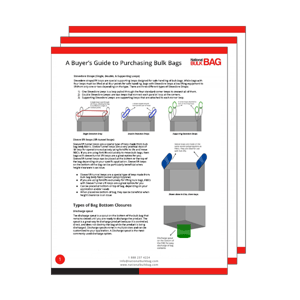
Download the guide by clicking below. By downloading, you'll learn all about:
- Types of bags
- Coated vs. uncoated
- Liners
- Bags with baffles
- Types of lift loops
- 5:1 & 6:1 safety guidelines
- Much more!
Click the button below to download our comprehensive buyer's guide.